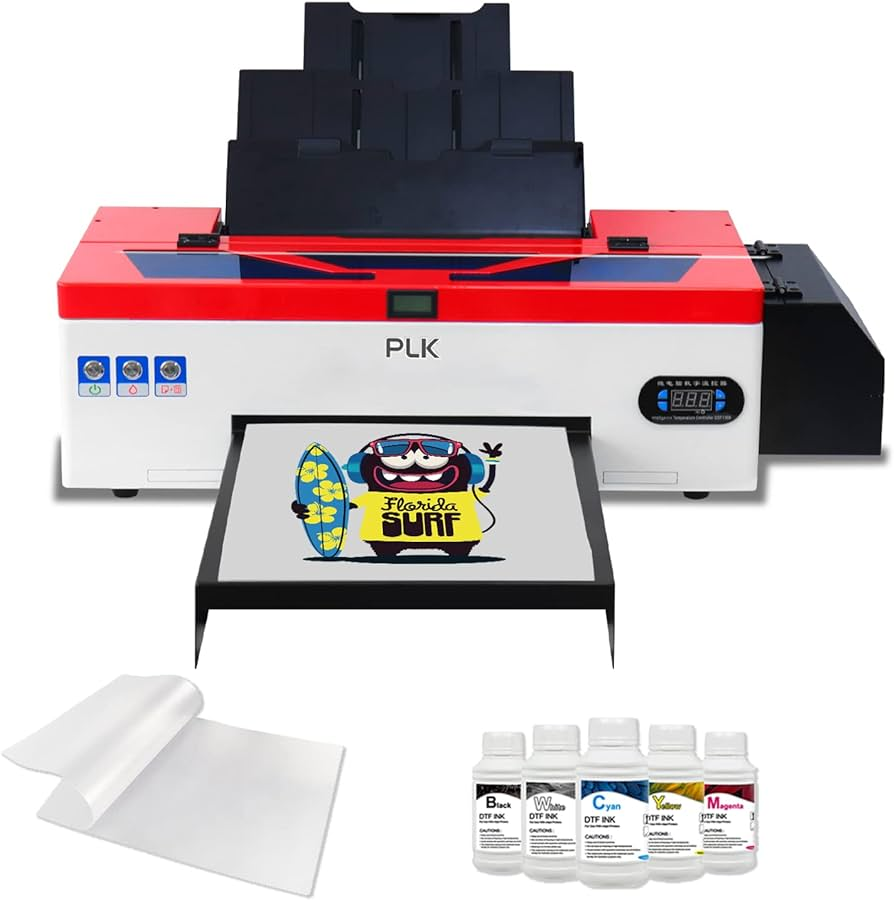
Eager to print your brilliant designs onto fabric but overwhelmed by the printing options? Exploring new technologies like direct-to-film (DTF) printing and proven ones like screen printing and dye sublimation makes choosing confusing. However, understanding the capabilities and limitations of each empowers you to select the optimal textile printing method for your creative vision. We’ll compare DTF against conventional fabric printing across factors like setup costs, process complexity, customization capabilities, print longevity, and material support. Read on for an insider’s overview of how DTF stacks up against traditional techniques, so you make an informed decision for your next textile project.
Lower entry costs
Conventional printing relies on serious equipment investments before launching production. Screen printing needs frames, exposure units, washout booths, and drying racks. Sublimation requires heat presses and specialty coatings. However, DTF leverages affordable digital inkjet printers that mirror conventional desktop units. Without this equipment burden, DTF allows bootstrapping your custom fabric endeavors.
Simplified workflow
Both screen printing and sublimation involve multi-step pre-production workflows around color separation, press setup/calibration, curing tests, etc. But DTF leverages a direct computer-to-printer workflow to output prints immediately with no physical setup. Send your print-ready file and watch fabrics roll off the press moments later. This simplified process helps new creators get to printing faster.
Unlimited customization
Want 50 shirts with 50 unique designs? No problem with DTF printers. Digital workflows effortlessly handle any variation in imagery, patterns, sizes, and colors. But screen printing requires mixing custom inks and cutting unique screens to support each variation inefficient for one-off designs. Sublimation needs custom-cut transfer sheets per design as well. Minimal setup waste makes DTF extremely competitive for small batch production like samples and prototypes. Twelve unique shirts cost nearly the same to print as twelve identical ones thanks to fast digital workflow. It grants unprecedented flexibility for iterating before investing in mass production.
Print durability
For color vibrancy and crispness, a dialed-in DTF printer rivals even exceptional screen prints. Advanced inks and fabric pretreatments also achieve wash durability by closing in on screen printing. All without thick ink layers that alter fabric hand feel and breathability. DTF’s Achilles heel is its narrow fabric support for now. Polyester and poly-blends yield excellent results, but temperamental performance on natural fibers has limited adoption. If cotton capability is crucial, screen printing remains the supple and reliable choice. But, DTF por metros material support is steadily improving.
Screen printing
DTF printing goes toe-to-toe with conventional textile printing technologies across most considerations from cost to image quality to customization flexibility. The promise of easily accessible digital printing helps democratize fabric customization once restricted only to industrial players. For makers and designers focused on easy iteration, full customization even in small batches, and skipping tedious setup workflows, DTF checks all the right boxes. Digital native creators who value design velocity from concept to physical print choose DTF for its agility and responsiveness augmenting their creative process.
If your ambitions demand the creative freedom to instantly translate striking concepts into one-off custom textile pieces, DTF grants your fabric wishes thanks to its digital backbone absent of physical constraints. By merging design agility with manufacturing flexibility, direct-to-film printing opens new doors for textile entrepreneurs and empowers designers to achieve more success.